A Comprehensive Guide to Spray Guns: Understanding the Differences
— BIGTOYO MACHINERY
Spray guns are tools that utilize compressed air or liquid to rapidly release a substance, often paint or other coatings, onto a surface. They provide a uniform application of the coating and are commonly used in various industries for finishing and coating applications. Depending on the paint feeding modes and atomization, spray guns are further divided into multiple types.
To explore the principles, advantages, and applications of electrostatic coating, visit Goodbye to Traditional Spray Painting! Electrostatic Painting Machine: The Key to Automated Coating.
The gravity feed spray gun utilizes a paint cup positioned above the gun, relying on gravity to feed the paint into the nozzle. When the trigger is pressed, compressed air flows at high speed through the nozzle, creating negative pressure that draws paint from the cup and atomizes it. At the nozzle, the paint mixes with the high-speed air, forming fine mist-like particles that are evenly sprayed onto the surface. This process allows for smooth and uniform coating, with adjustable spray patterns and thickness.
- Advantages:
- Ideal for small-scale spraying, as minimal paint remains in the cup.
- Easy to clean and switch colors, offering excellent mobility.
- Disadvantages:
- The top-mounted cup can obstruct the operator’s view, and the smaller paint flow may affect spray consistency.
- Limited paint cup capacity requires frequent refills, making it unsuitable for large-scale applications.
In a siphon-feed spray gun, the paint cup is located below the gun, and high-speed airflow creates negative pressure at the nozzle, drawing paint upward through a siphon effect. Once the paint reaches the nozzle, it mixes with the high-speed air, breaking into fine particles to form an even spray mist. The atomized paint is then propelled toward the surface, creating a uniform layer. Operators can adjust air pressure and nozzle settings to control the spray coverage and coating thickness for various applications.
- Advantages:
- Larger paint cup capacity is suitable for extensive applications and provides excellent atomization.
- Stable operation with the paint cup positioned below the gun.
- Disadvantages:
- Prolonged use can cause operator fatigue.
- Cleaning is more challenging due to paint residue in the cup.
Pressure-feed spray guns are designed for large-scale, high-intensity applications, such as industrial production lines, vehicle coatings, and large equipment spraying. Paint is stored in a separate pressure tank or container, which is pressurized using compressed air or pump systems to provide a continuous paint supply to the spray gun. The pressurized paint is delivered through hoses to the nozzle, where it mixes with compressed air for atomization, producing fine mist particles that ensure consistent spray coverage. Operators can adjust the pressure in the tank and gun to control the flow rate, spray pattern, and coating thickness, making this system highly adaptable to various large-scale coating needs.
- Advantages:
- Suitable for long-distance spraying and large surfaces with excellent atomization.
- Lighter gun handling due to the external paint container.
- Ideal for continuous production lines with infrequent color changes.
- Disadvantages:
- Time-consuming cleaning and color changes.
- Higher costs due to the need for additional pressure tanks or pumps.
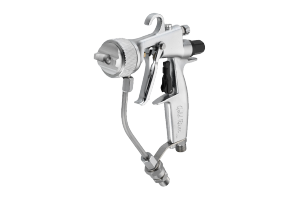
AA Manual Spray Gun
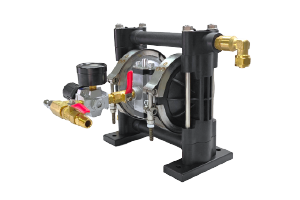
1:1 Air Diaphragm Pump
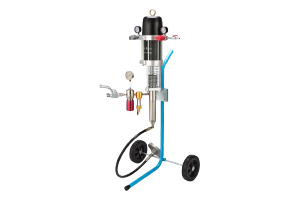
20:1 Air Piston Pump
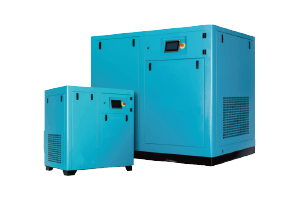
Industrial Air Compressor
Atomization greatly affects spray quality, influencing particle size, distribution, and coating smoothness. Based on atomization principles, spray guns can be divided as follows:
Air Spray Guns compress air to atomize paint. Variants include HVLP, LVMP, and LVLP, offering different levels of air pressure and paint flow for optimal results.
HVLP (High Volume Low Pressure)
Operates at high air volume and low pressure for fine mist particles and strong paint adhesion.
- Advantages:
- High transfer efficiency with minimal overspray.
- Produces smooth finishes, suitable for detailed work.
- Environmentally friendly with reduced paint waste.
- Disadvantages:
- Higher cost due to the need for powerful air compressors.
- Slower spray speed, making it less efficient for large areas.
LVMP (Low Volume Medium Pressure)Lower air consumption with medium pressure, balancing atomization quality and efficiency.
- Advantages:
- Fine atomization and reduced air compressor demand.
- Cost-effective with lower paint waste.
- Disadvantages:
- Requires skilled operators for optimal results.
LVLP (Low Volume Low Pressure)Very low air consumption with efficient nozzle design for fine atomization.
- Advantages:
- Produces uniform, high-quality coatings.
- Works with smaller compressors, reducing operating costs.
- Disadvantages:
- Narrow spray coverage may increase time for medium-scale tasks.
Type | Conventional | HVLP | LVMP | LVLP |
Air Flow | High | High | Low | Low |
Air Pressure | High | Low | Medium | Low |
Atomization | Medium | Excellent | Excellent | Superior |
Transfer Efficiency | Low | Medium | Medium | High |
Application | Large-scale industrial and architectural painting applications | Widely applicable to various small and medium-sized painting operations | Medium to small-scale precision painting, such as automotive repair and furniture finishing | Precision painting, demanding higher coating quality |
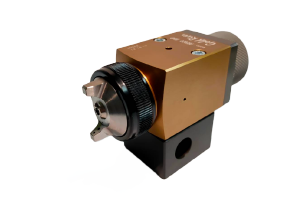
Auto Air Spray Gun
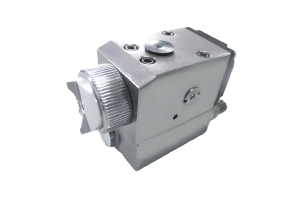
AA Auto Spray Gun
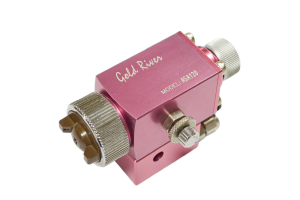
Auto LVMP Air Spray Gun
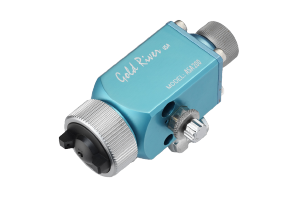
Auto LVLP Air Spray Gun
Paint is directly pressurized and ejected through a fine nozzle at high speed, atomizing the paint into particles.
- Advantages:
- High spraying efficiency, suitable for large areas with thick coatings.
- Disadvantages:
- Transfer efficiency is low.
- Atomization is not adequate compared to air-assisted systems.
Air-Assisted Airless Spray GunCombines airless spray with a small amount of compressed air for finer atomization.
- Advantages:
- Provides a balance between efficiency and atomization quality.
- Reduces overspray, improving paint utilization.
- Disadvantages:
- Compared to airless spray guns, the investment cost is higher.
- Offers more precise spray patterns and fan size control, demanding higher operator skills.
Item | Airless Spray Gun | Air-Assisted Airless Spray Gun |
Atomization | Atomized paint particles are larger, providing strong coverage but potentially resulting in a rougher surface. | The spray is fine and uniform, suitable for high-quality requirements. |
Transfer Efficiency | Relatively low, with some overspray causing waste. | Relatively high, with more uniform atomization and less overspray, improving utilization. |
Spraying Efficiency | Fast spraying speed, suitable for large-area, thick coating operations. | Relatively slower spraying speed, but paint flow can be controlled, suitable for fine operations. |
Equipment Cost | Relatively low, with simpler equipment. | Relatively high, with more complex equipment, including an air compressor. |
Application | Large-area, thick coating operations, such as walls and steel structures. | Requires fine coatings and high-quality requirements, such as automobiles and furniture. |

Manual Electrostatic Spray Gun
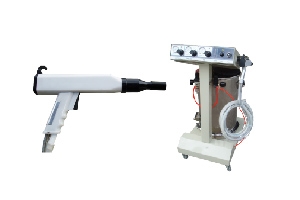
Manual Powder Electrostatic Spray Gun
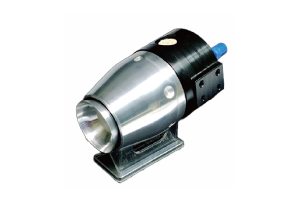
Super Micro Bell Sprayer
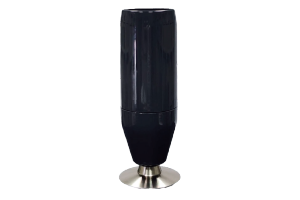
Turbo Disc Sprayer
Electrostatic Spray GunsUses an electrostatic field to charge paint particles, which are attracted to oppositely charged surfaces for uniform coverage.
- Advantages:
- Electrostatic spray guns attract paint particles, causing them to adhere more effectively to the workpiece surface, reducing waste and overspray, and thereby improving paint utilization.
- The electrostatic attraction can help paint adhere better to irregular or complex-shaped objects, ensuring a uniform coating.
- Electrostatic spraying produces a fine, uniform spray, providing a smooth and consistent coating quality, especially suitable for applications requiring high-quality surface finishes.
- Electrostatic spraying has lower volatile organic compound (VOCs) emissions, causing relatively less environmental impact and meeting modern environmental requirements.
- Due to the high efficiency of electrostatic spray guns, it can shorten the spraying time and improve production efficiency.
- Electrostatic spray guns are suitable for workpieces of various materials, such as metals, plastics, and wood, and can spray various paints and powders.
- Disadvantages:
- High initial equipment costs.
- Requires skilled operation.
Conclusion
With numerous spray gun options available, selecting the right one depends on your specific coating needs. Consider factors like material to be sprayed, spray pattern, application area, desired finish, and environmental regulations to choose the most suitable spray gun for optimal results.Reminder:If you are interested in the BigToyo spray gun series, click here to learn more about our product details. Feel free to contact us anytime, and we will provide you with the most professional service.